Nej, det bliver ærligt talt ikke kedeligt – især ikke hvis du elsker elastiske gummiting. Hvis du læser videre, vil du finde ud af næsten alt, hvad du nogensinde har ønsket at vide om enkomponents silikoneforseglinger.
1) Hvad de er
2) Hvordan man laver dem
3) Hvor skal de bruges
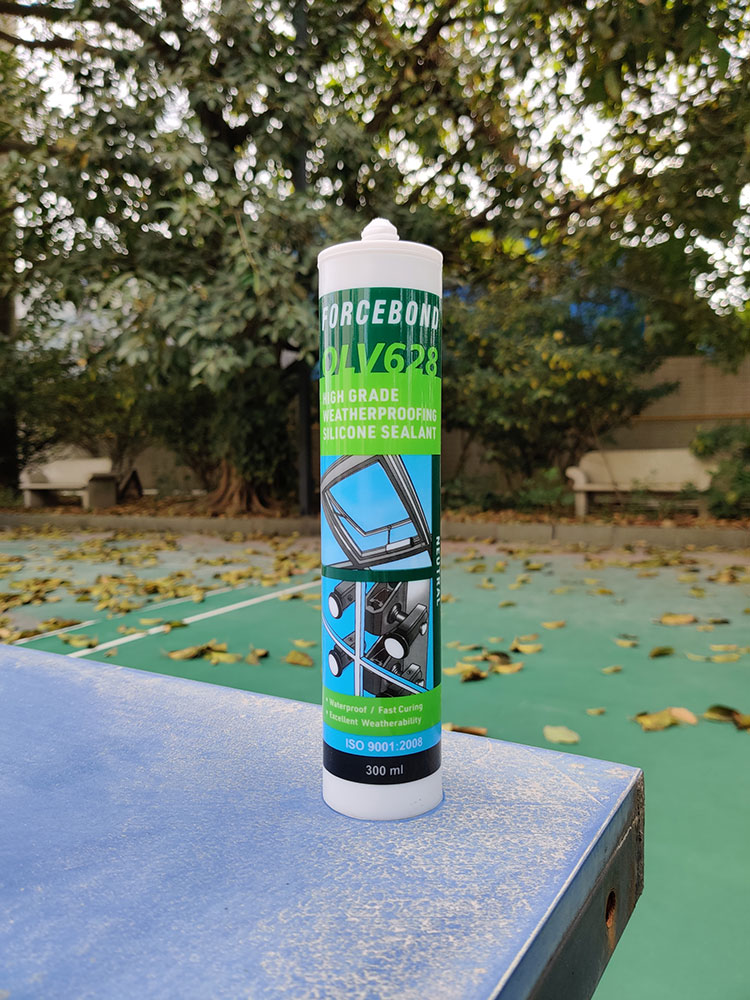
Indledning
Hvad er en en-komponent silikoneforsegling?
Der findes mange typer kemisk hærdende fugemasser – silikone, polyurethan og polysulfid er de mest kendte. Navnet stammer fra rygraden af de involverede molekyler.
Silikone-rygraden er:
Si – O – Si – O – Si – O – Si
Modificeret silikone er en ny teknologi (i hvert fald i USA) og betyder faktisk en organisk rygrad hærdet med silankemi. Et eksempel er alkoxysilantermineret polypropylenoxid.
Alle disse kemiske sammensætninger kan enten bestå af én eller to dele, hvilket naturligvis afhænger af antallet af dele, du skal bruge for at få materialet til at hærde. Derfor betyder én del blot, at du skal åbne røret, patronen eller spanden, og så hærder dit materiale. Normalt reagerer disse én-komponentsystemer med luftfugtigheden og bliver til gummi.
Så en en-komponent silikone er et system, der er stabilt i røret, indtil det ved udsættelse for luft hærder og producerer en silikonegummi.
Fordele
Enkomponents silikoner har mange unikke fordele.
- Når de blandes korrekt, er de meget stabile og pålidelige med fremragende vedhæftning og fysiske egenskaber. En holdbarhed (den tid, du kan lade dem være i tuben, før du bruger dem) på mindst et år er normal, og nogle formuleringer holder i mange år. Silikoner har også uden tvivl den bedste langsigtede ydeevne. Deres fysiske egenskaber ændrer sig næsten ikke over tid uden effekt fra UV-eksponering, og derudover udviser de fremragende temperaturstabilitet, der overgår andre fugemassers med mindst 50 ℃.
- Enkomponents silikoner hærder relativt hurtigt, og danner typisk en hinde inden for 5 til 10 minutter, bliver klæbefri inden for en time og hærder til en elastisk gummi, der er ca. 3 mm dyb, på mindre end en dag. Overfladen har en dejlig gummiagtig fornemmelse.
-Da de kan gøres gennemskinnelige, hvilket er en vigtig egenskab i sig selv (gennemskinnelig er den mest anvendte farve), er det relativt nemt at pigmentere dem til enhver farve.
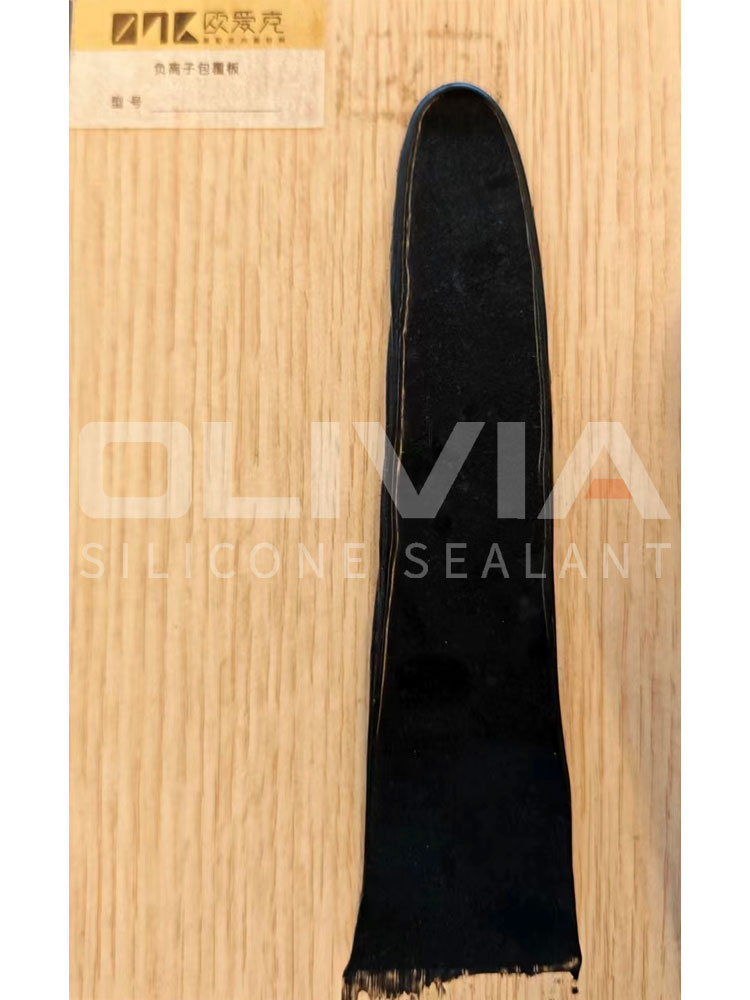
Begrænsninger
Silikoner har to hovedbegrænsninger.
1) De kan ikke males med vandbaseret maling - det kan også være vanskeligt med opløsningsmiddelbaseret maling.
2) Efter hærdning kan fugemassen frigive noget af sin silikoneblødgører, som, når den bruges i en bygnings ekspansionsfuge, kan skabe grimme pletter langs fugens kant.
Da systemet er i ét stykke, er det naturligvis umuligt at opnå en hurtig, dybdegående hærdning, fordi det skal reagere med luften og derfor hærder oppefra og ned. Lidt mere specifikt kan silikoner ikke bruges som eneste tætning i isolerede glasvinduer, fordi... Selvom de er fremragende til at holde flydende vand i store mængder ude, passerer vanddamp relativt let gennem den hærdede silikonegummi, hvilket får IG-enhederne til at dugge.
Markedsområder og anvendelser
Enkomponents silikoner bruges stort set overalt, inklusive, til nogle bygningsejeres store fortrydelse, hvor de to ovennævnte begrænsninger forårsager problemer.
Bygge- og gør-det-selv-markederne tegner sig for den største volumen, efterfulgt af bilindustrien, industrien, elektronikken og luftfarten. Som med alle fugemasser er silikonens hovedfunktion at klæbe og udfylde mellemrummet mellem to ens eller forskellige underlag for at forhindre vand eller træk i at trænge igennem. Nogle gange vil en formulering næppe ændres andet end at gøre den mere flydende, hvorpå den derefter bliver til en belægning. Den bedste måde at skelne mellem en belægning, et klæbemiddel og et fugemiddel er enkel. Et fugemiddel forsegler mellem to overflader, hvorimod en belægning dækker og beskytter kun én, mens et klæbemiddel i vid udstrækning holder to overflader sammen. Et fugemiddel minder mest om et klæbemiddel, når det bruges i strukturglas eller isolerede ruder, men det fungerer stadig til at forsegle de to underlag ud over at holde dem sammen.
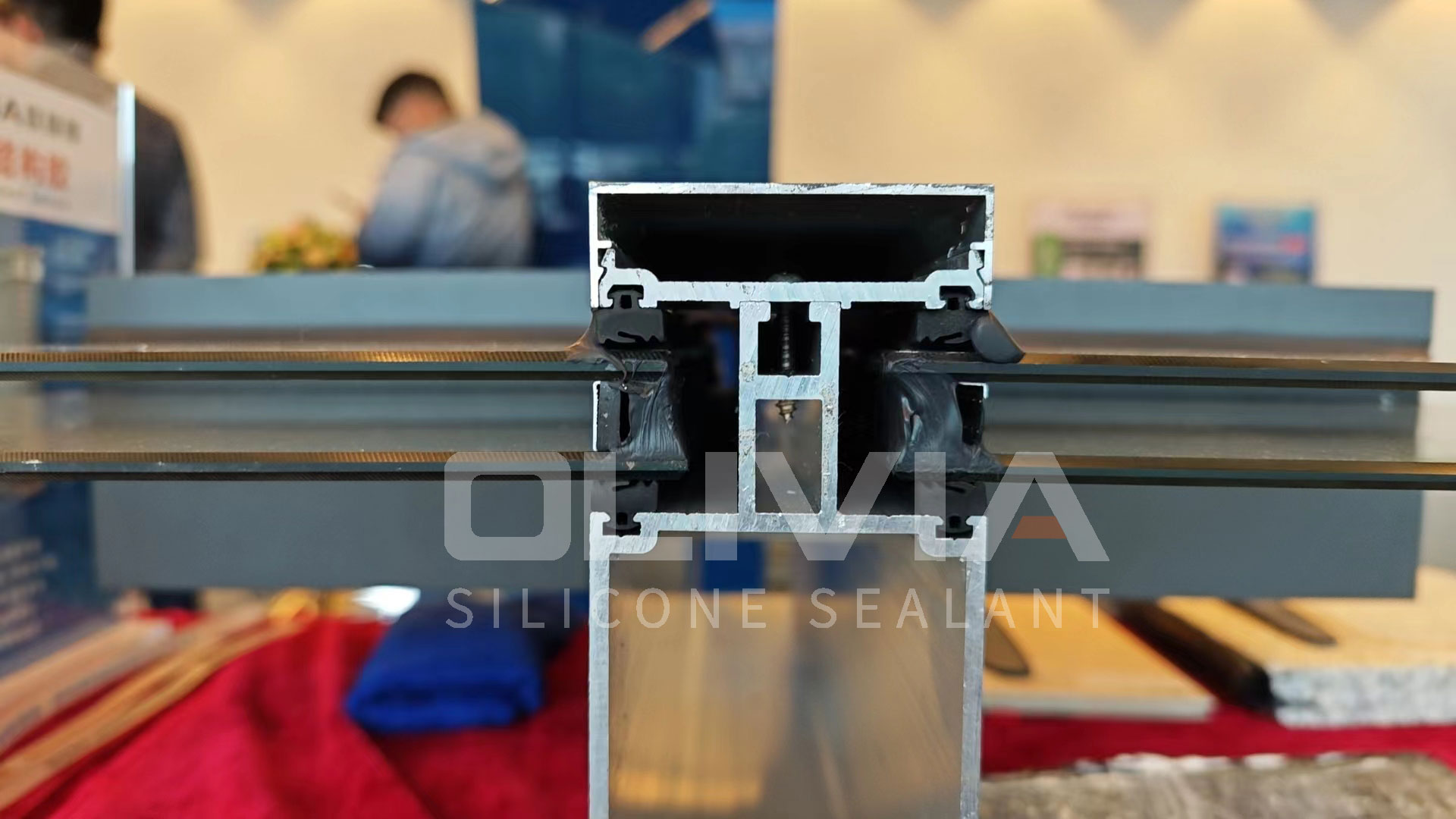
Grundlæggende kemi
Silikoneforseglingen ligner normalt i uhærdet tilstand en tyk pasta eller creme. Ved udsættelse for luft hydrolyserer de reaktive endegrupper i silikonepolymeren (reagerer med vand) og forbinder sig derefter med hinanden, hvorved vand frigives og der dannes lange polymerkæder, der fortsætter med at reagere med hinanden, indtil pastaen til sidst bliver til en imponerende gummi. Den reaktive gruppe i enden af silikonepolymeren kommer fra den vigtigste del af formuleringen (eksklusive selve polymeren), nemlig tværbinderen. Det er tværbinderen, der giver forseglingen dens karakteristiske egenskaber enten direkte, såsom lugt og hærdningshastighed, eller indirekte, såsom farve, vedhæftning osv., på grund af de andre råmaterialer, der kan anvendes med specifikke tværbindersystemer, såsom fyldstoffer og vedhæftningsfremmere. Valg af den rigtige tværbinder er nøglen til at bestemme forseglingens endelige egenskaber.
Hærdningstyper
Der findes flere forskellige hærdningssystemer.
1) Acetoxy (lugter af sur eddike)
2) Oxim
3) Alkoxy
4) Benzamid
5) Amin
6) Aminoxy
Oximer, alkoxier og benzamider (mere udbredt i Europa) er de såkaldte neutrale eller ikke-sure systemer. Aminer og aminooxysystemer har en ammoniaklugt og anvendes typisk mere i bil- og industriområder eller specifikke udendørs byggeriapplikationer.
Råvarer
Formuleringer består af flere forskellige komponenter, hvoraf nogle er valgfrie, afhængigt af den tilsigtede slutanvendelse.
De eneste absolut nødvendige råmaterialer er reaktiv polymer og tværbinder. Fyldstoffer, adhæsionsfremmere, ikke-reaktiv (blødgørende) polymer og katalysatorer tilsættes dog næsten altid. Derudover kan mange andre tilsætningsstoffer anvendes, såsom farvepastaer, fungicider, flammehæmmere og varmestabilisatorer.
Grundlæggende formuleringer
En typisk oximkonstruktion eller gør-det-selv-fugemasseformulering vil se nogenlunde sådan ud:
% | ||
Polydimethylsiloxan, OH-termineret 50.000 cps | 65,9 | Polymer |
Polydimethylsiloxan, trimethyltermineret, 1000 cps | 20 | Blødgører |
Methyltrioximinosilan | 5 | Tværbinder |
Aminopropyltriethoxysilan | 1 | Adhæsionsfremmer |
150 kvm/g overfladeareal af pyrogen silica | 8 | Fyldstof |
Dibutyltindilaurat | 0,1 | Katalysator |
Total | 100 |
Fysiske egenskaber
Typiske fysiske egenskaber omfatter:
Forlængelse (%) | 550 |
Trækstyrke (MPa) | 1.9 |
Modul ved 100 forlængelse (MPa) | 0,4 |
Shore A-hårdhed | 22 |
Hud over tid (min) | 10 |
Tid til frigørelse af tackle (min) | 60 |
Skrabetid (min) | 120 |
Gennemhærdning (mm på 24 timer) | 2 |
Formuleringer, der bruger andre tværbindere, vil ligne hinanden, måske med forskel i niveauet af tværbinder, typen af adhæsionsfremmer og hærdningskatalysatorer. Deres fysiske egenskaber vil variere en smule, medmindre der er involveret kædeforlængere. Nogle systemer kan ikke fremstilles let, medmindre der anvendes en stor mængde kridtfyldstof. Disse typer formuleringer kan naturligvis ikke produceres i den klare eller gennemskinnelige type.
Udvikling af fugemasser
Der er 3 trin i udviklingen af en ny fugemasse.
1) Koncept, produktion og test i laboratoriet - meget små volumener
Her får laboratoriekemikeren nye ideer og starter typisk med en manuel blanding af omkring 100 gram fugemasse for at se, hvordan det hærder, og hvilken slags gummi der produceres. Nu er der en ny maskine tilgængelig, "The Hauschild Speed Mix", fra FlackTek Inc. Denne specialiserede maskine er ideel til at blande disse små 100 g batcher på få sekunder, mens den udstøder luft. Dette er vigtigt, da det nu giver udvikleren mulighed for rent faktisk at teste de fysiske egenskaber af disse små batcher. Pyrolyse eller andre fyldstoffer, såsom udfældet kridt, kan blandes i silikonen på omkring 8 sekunder. Afluftning tager omkring 20-25 sekunder. Maskinen fungerer ved hjælp af en dobbelt asymmetrisk centrifugemekanisme, der grundlæggende bruger partiklerne selv som deres egne blandearme. Den maksimale blandingsstørrelse er 100 gram, og der findes flere forskellige koptyper, herunder engangs, hvilket betyder absolut ingen rengøring.
Nøglen i formuleringsprocessen er ikke kun typen af ingredienser, men også rækkefølgen af tilsætning og blandetid. Naturligvis er udelukkelse eller fjernelse af luft vigtig for at sikre produktets holdbarhed, da luftbobler indeholder fugt, som derefter vil få fugemassen til at hærde indefra.
Når kemikeren har fundet den type fugemasse, der kræves til den specifikke anvendelse, skaleres der op til en 1-liters planetblander, som kan producere omkring 3-4 små rør på 110 ml (3 oz). Dette er tilstrækkeligt materiale til den indledende holdbarhedstest og vedhæftningstest samt eventuelle andre særlige krav.
Derefter kan han gå til en maskine på 1 eller 2 gallon for at producere 8-12 rør à 10 oz til mere dybdegående test og kundeprøvetagning. Forseglingen ekstruderes fra beholderen gennem en metalcylinder ind i patronen, der passer over emballagecylinderen. Efter disse test er han klar til opskalering.
2) Opskalering og finjustering af mellemstore volumener
I opskaleringen produceres laboratorieformuleringen nu på en større maskine, typisk i området 100-200 kg eller omkring en tønde. Dette trin har to hovedformål.
a) at se om der er nogen signifikante ændringer mellem 4 lb-størrelsen og denne større størrelse, som kan skyldes blandings- og dispersionshastigheder, reaktionshastigheder og forskellige mængder af forskydning i blandingen, og
b) at producere nok materiale til at stikprøveudvælge potentielle kunder og få reel feedback fra jobbet.
Denne 50-gallons maskine er også meget nyttig til industriprodukter, når der kræves lave mængder eller specialfarver, og der kun skal produceres omkring én tromle af hver type ad gangen.
Der findes flere typer blandemaskiner. De to mest almindeligt anvendte er planetariske blandere (som vist ovenfor) og højhastighedsdispergeringsmaskiner. En planetarisk blander er god til blandinger med højere viskositet, hvorimod en dispergeringsmaskine fungerer bedre, især i flydende systemer med lavere viskositet. I typiske byggeforseglinger kan begge maskiner bruges, så længe man er opmærksom på blandetiden og den potentielle varmeudvikling fra en højhastighedsdispergeringsmaskine.
3) Produktionsmængder i fuld skala
Den endelige produktion, som kan være batch- eller kontinuerlig, reproducerer forhåbentlig blot den endelige formulering fra opskaleringstrinnet. Normalt produceres en relativt lille mængde (2 eller 3 batcher eller 1-2 timers kontinuerlig produktion) materiale først i produktionsudstyret og kontrolleres, før normal produktion starter.
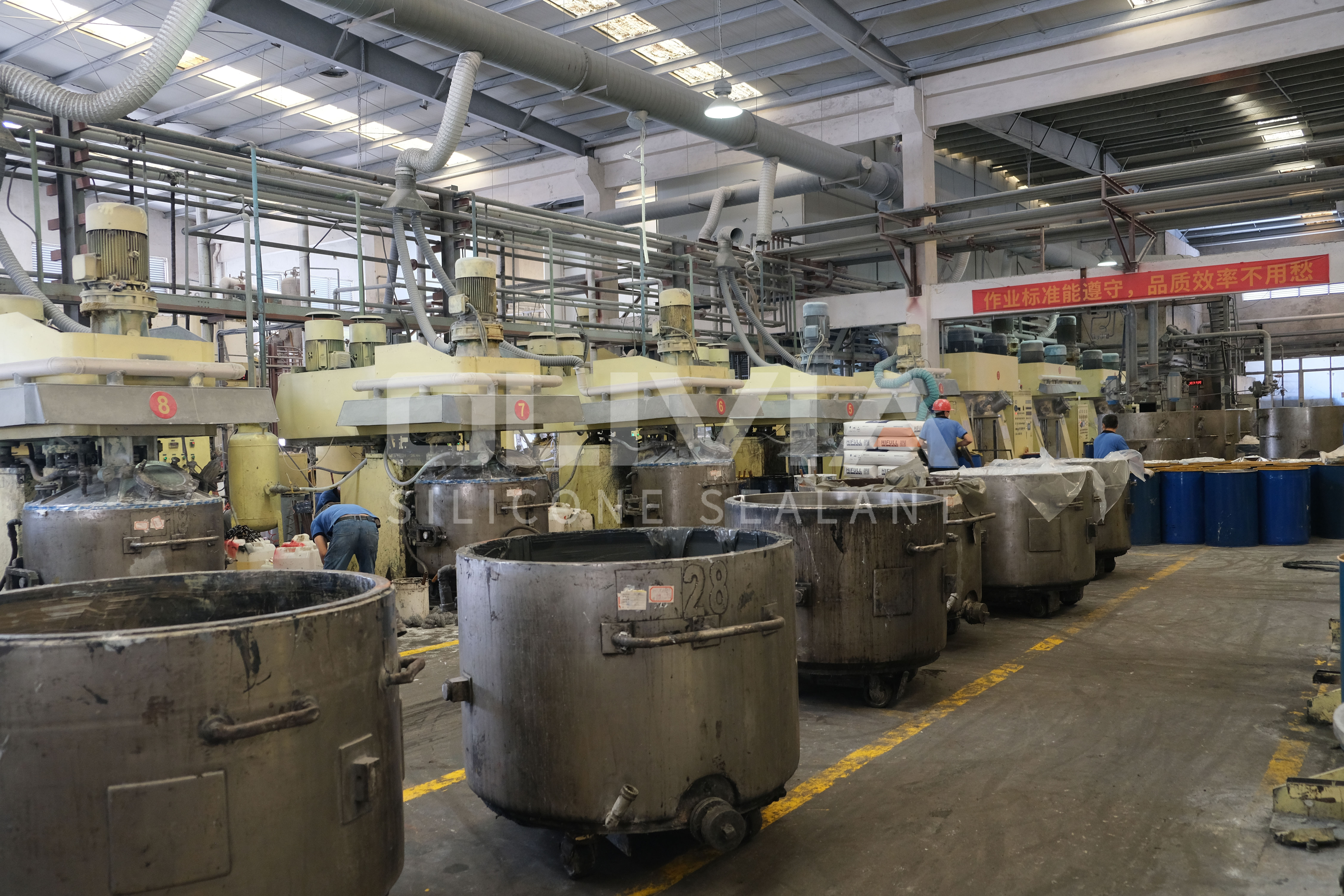
Testning - Hvad og hvordan man tester.
Hvad
Fysiske egenskaber - Forlængelse, trækstyrke og modul
Vedhæftning til passende underlag
Holdbarhed - både accelereret og ved stuetemperatur
Hærdningsrater - Skin over tid, klæbefri tid, ridsetid og gennemhærdning, farver Temperaturstabilitet eller stabilitet i forskellige væsker såsom olie
Derudover kontrolleres eller observeres andre vigtige egenskaber: konsistens, lav lugt, korrosivitet og generelt udseende.
Hvordan
Et ark fugemasse trækkes ud og lades hærde i en uge. En speciel håndvægt skæres derefter ud og placeres i en træktester for at måle fysiske egenskaber såsom forlængelse, modul og trækstyrke. De bruges også til at måle vedhæftnings-/kohæsionskræfter på specielt forberedte prøver. Enkle ja-nej vedhæftningstests udføres ved at trække i perler af materiale, der er hærdet på de pågældende substrater.
Et Shore-A-måler måler gummiets hårdhed. Denne enhed ligner en vægt og en måler med en spids, der presser ind i den hærdede prøve. Jo mere spidsen trænger ind i gummiet, desto blødere er gummiet og desto lavere er værdien. En typisk byggefugemasse vil ligge i området 15-35.
Hudovergangstider, klæbefri tider og andre specielle hudmålinger udføres enten med fingeren eller med plastikplader med vægte. Tiden, før plastikken kan trækkes rent af, måles.
For at opnå holdbarhed ældes tuber med fugemasse enten ved stuetemperatur (hvilket naturligt tager 1 år at opnå) eller ved forhøjede temperaturer, typisk 50 ℃, i 1, 3, 5, 7 uger osv. Efter ældningsprocessen (i det accelererede tilfælde afkøles tuben) ekstruderes materialet fra tuben og trækkes ind i en plade, hvor det hærder. De fysiske egenskaber af den gummi, der dannes i disse plader, testes som før. Disse egenskaber sammenlignes derefter med egenskaberne af friskblandede materialer for at bestemme den passende holdbarhed.
En specifik og detaljeret forklaring af de fleste nødvendige tests kan findes i ASTM-håndbogen.
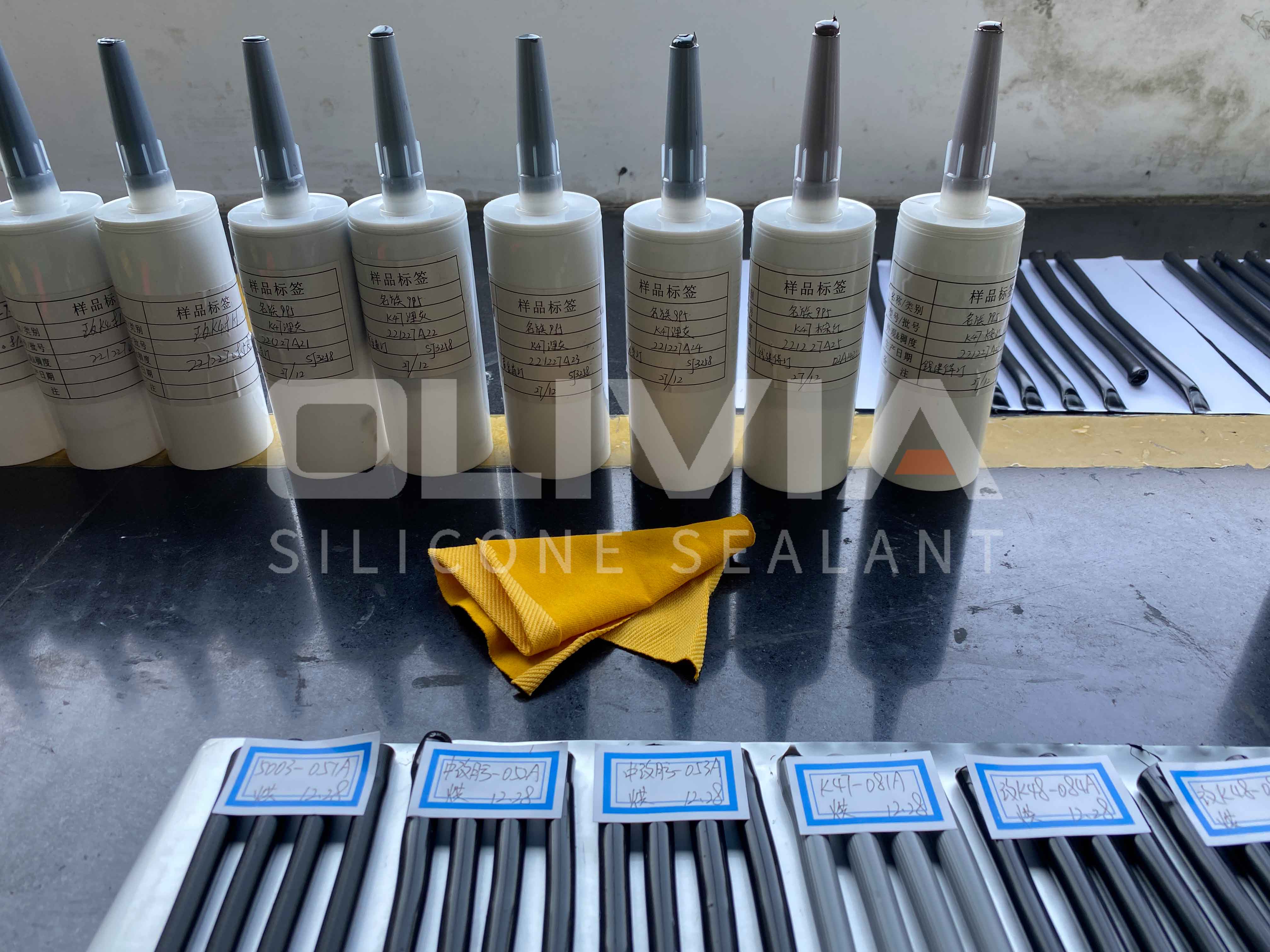
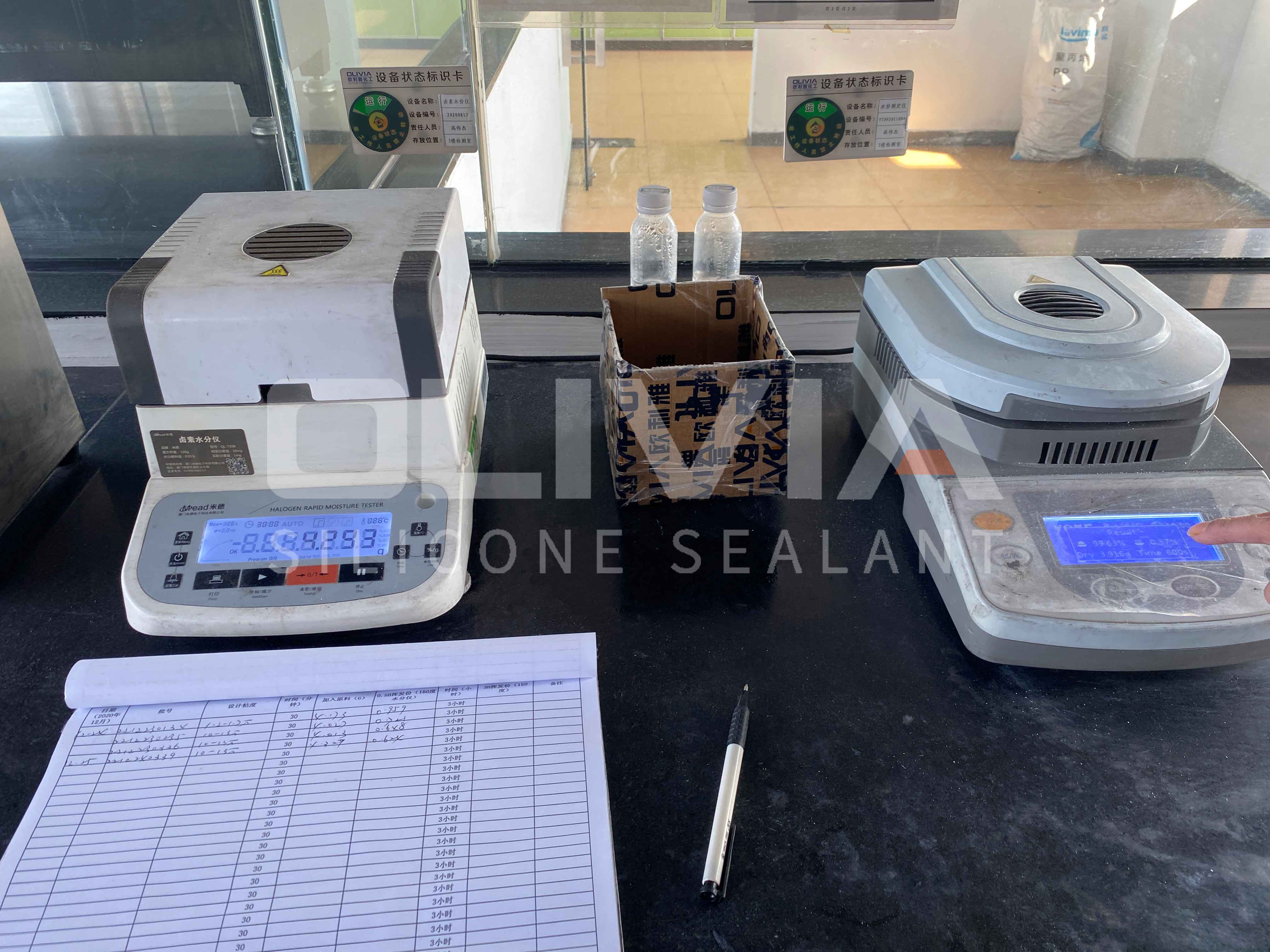
Nogle afsluttende tips
Enkomponents silikoner er de højeste kvalitetsforseglinger på markedet. De har dog begrænsninger, og hvis der stilles specifikke krav, kan de udvikles specielt.
Det er vigtigt at sikre, at alle råmaterialerne er så tørre som muligt, at formuleringen er stabil, og at luften fjernes i produktionsprocessen.
Udvikling og testning er stort set den samme proces for enhver komponent fugemasse uanset type – sørg blot for at have kontrolleret alle mulige egenskaber, før du begynder at producere mængder, og at du har en klar forståelse af applikationens behov.
Afhængigt af anvendelseskravene kan den korrekte hærdningskemi vælges. Hvis der f.eks. vælges silikone, og lugt, korrosion og vedhæftning ikke anses for vigtige, men der er behov for en lav pris, er acetoxy den rigtige løsning. Men hvis der er tale om metaldele, der kan være korroderede, eller hvis der kræves en særlig vedhæftning til plastik i en unik blank farve, har du brug for en oxim.
[1] Dale Flackett. Siliciumforbindelser: Silaner og silikoner [M]. Gelest Inc: 433-439
* Foto fra OLIVIA Silikoneforsegling
Opslagstidspunkt: 31. marts 2024